在某知名汽车整车厂焊接车间,每一道焊点都承载着该企业对精细工艺的坚守和对优质产品的追求。凭借2000余个焊点、90%的自动化率和200台精密设备,该企业基本实现了焊接过程的全自动化。然而,如何甄别出不良焊点,如何进行持续优化提升呢?树根互联结合自身在和ai算法上多年的技术沉淀,结合企业丰富的业务知识,双方共创,实现了焊点质量自动检测。
1、困境
汽车白车身焊点众多,质量管理压力山大。传统焊装领域焊点品质采用半破坏性抽检的方法检测焊点质量,存在3个问题:
1、影响焊接质量的要素多,依靠人力确认焊接要素,耗费时间长,效率低
2、焊点数量多,投入检查员多达20余人,全年累计投入2000余小时进行参数检查,仍无法全面监控准确的焊接质量
3、现有焊接数据无法被进一步开发利用。设备最多存储3000条焊接数据,旧数据不断被产生的新数据迭代,焊接数据与车身号没办法一一匹配,无法追溯
如何实现焊接数据的有效采集、存储、分析及管理,一度给该企业带来巨大困扰!
2、破局
针对上述问题,树根互联与该企业开展了专项合作,给其提供了“焊接ai质量在线智能检测”凯时国际的解决方案:
针对上述问题,树根互联与该企业开展了专项合作,给其提供了“焊接ai质量在线智能检测”凯时国际的解决方案:
针对焊接车间中已有的现场焊机,采集焊接数据以及plc数据,将数据通过工厂5g网络传输并存储至该企业iot平台,通过iot平台布置的人工智能算法实现对焊接工艺参数和运行数据的监测,对焊接的焊接质量进行在线检测,全面提升检测效率和质检准确性,明确以下4大建设目标:
1、焊接数据可集中管理:将所有焊接数据从分散的控制器中采集、并集中管理起来,实现远程集中监控
2 、焊接质量可实时监控:实时显示焊接结果状态,以及对应的过程数据(电阻、电流、焊接时间、热量等),出现问题及时提醒。
3、焊接过程异常可精准定位:根据焊接过程数据,基于统计分析和ai算法,分析判断引起工艺质量问题的深层次原因,比如某一把焊枪、某一个程序号频繁出现焊接问题。
4、焊接质量可长期溯源:建立每台车辆的焊接档案,长期保存带车辆id标签的焊接数据,一旦出现质量问题,有据可查。
3、方法
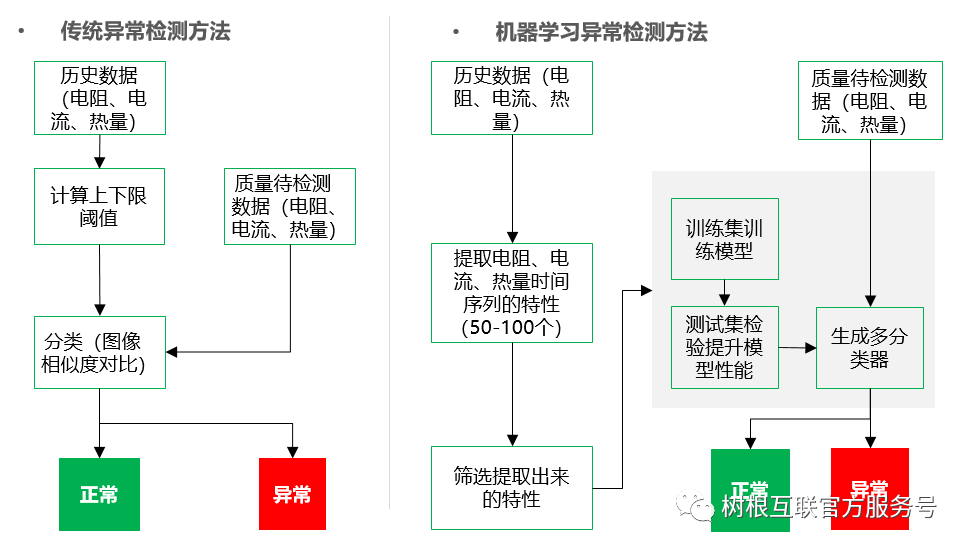
3、方法
通过采集现场实时焊接过程数据以及车辆属性数据,实现数据集中存储,并结合焊接质量检测模型,实现焊接正常/异常情况自动判断。实现对全数焊点100%检查,并建立每台车辆的可追溯焊接质量档案。
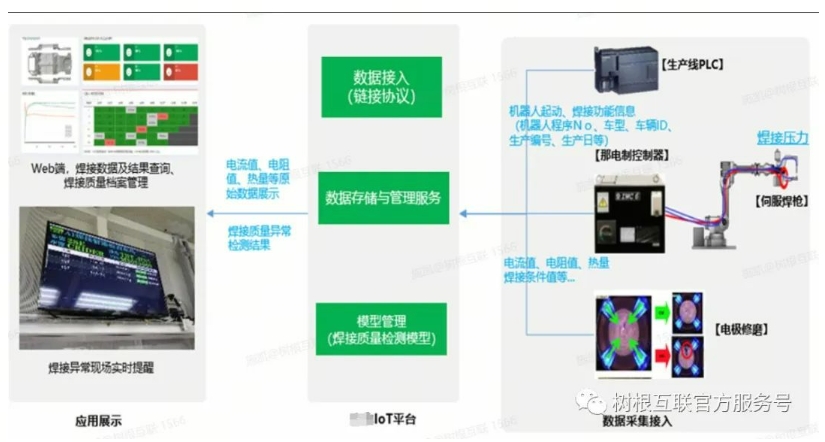
1、数据采集
现场共计35台独立的焊接设备控制器,相互之间未联网,综合数据采集成本,需首先构建4组小型局域网将焊接控制器数据和汇总至4台交换机。再分别从4台交换机加装边缘智能网关,通过5g将数据汇总至该企业iot平台统一存储。
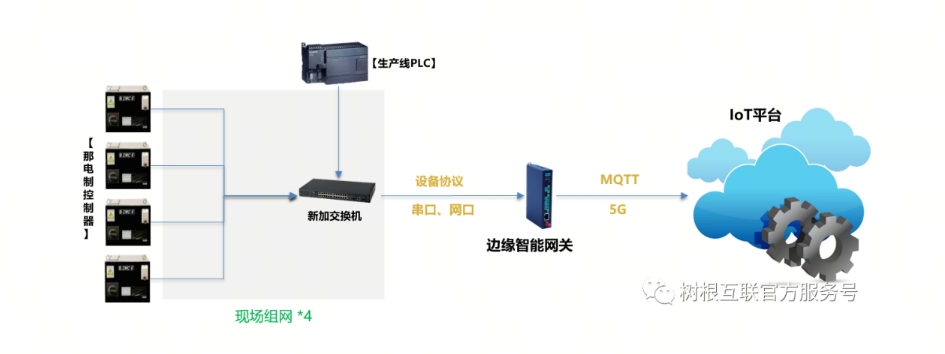
2、焊接质量模型构建
本项目除焊接数据采集集中存储、可视化展示外,还加入基于机器学习的算法模型,实现部分焊接质量问题自动判断。we部门业务人员已收集约百余组焊接过程数据,并逐一做标签分类,用于ai算法模型构建。模型构建步骤如下:
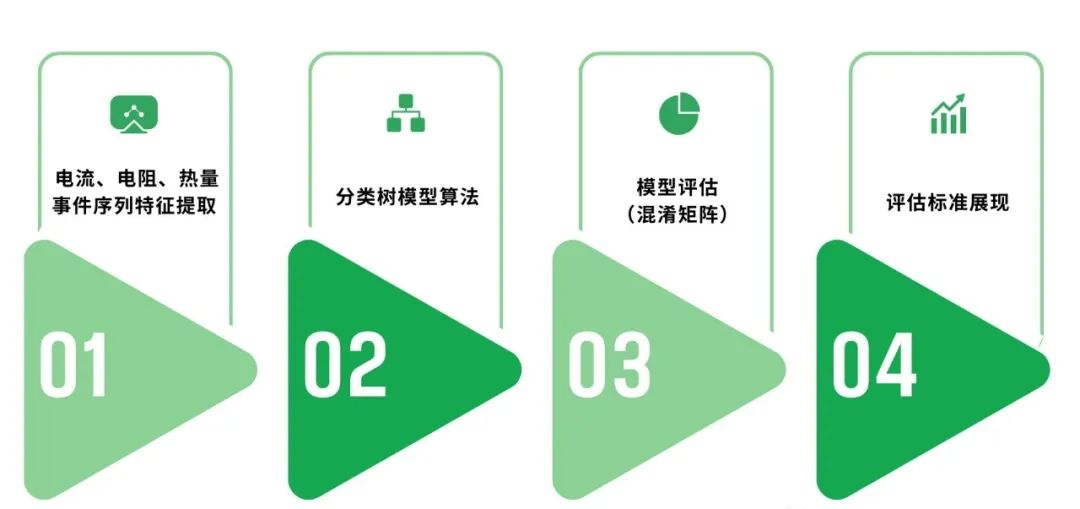
焊接质量检测模型探索性验证-数据可视化分析
将正常与异常焊接数据形成可视化对比,可以发现正常与异常数据大部分有明显边界区分,因此可以通过电阻、电流等工作参数来做焊接异常检测。但部分正常与异常与相互交织,很难通过传统的参数阈值设置来进行区分,而机器学习算法能够在相互交织的时间序列数据中剥离出差异,进而对正常和异常进行区分,因此需采用基于机器学习算法建模。
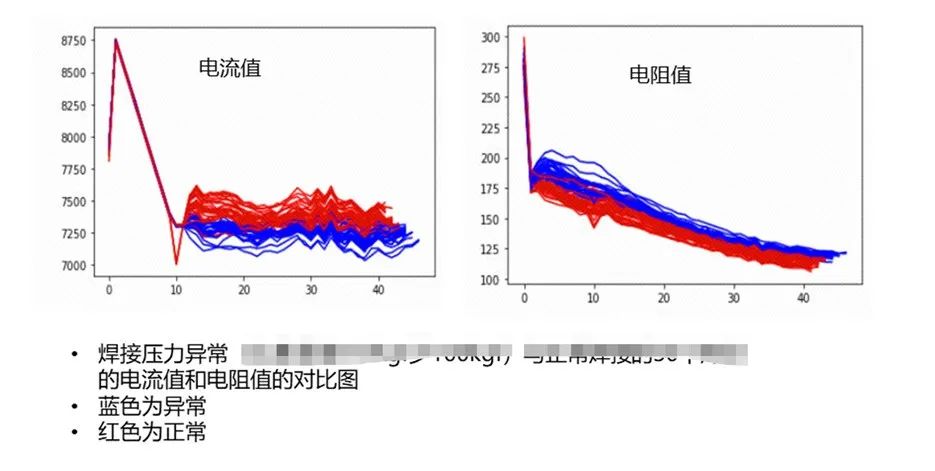
焊接质量检测模型探索性验证-机器学习算法建模
机器学习是通过树模型、线性模型或其他模型精确分离数值。本次焊接质量检测模型算法验证过程中,针对电阻、电流、热量数据共选取百余个特征数据,用于算法模型构建。
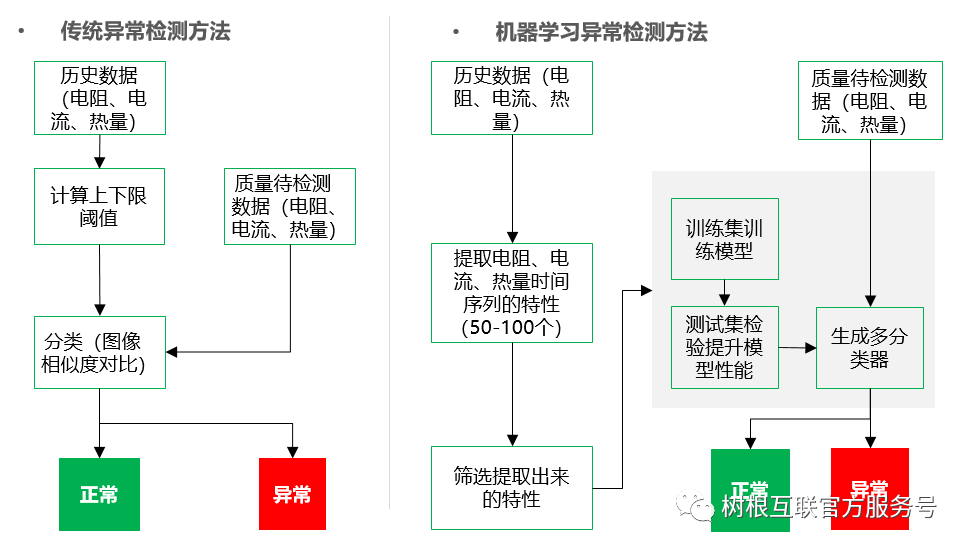
4、成效
通过ai技术对焊接过程中的电阻、电流、热量进行实时监控,提高了焊接质量的判断准确率,达到了83%-85%,大大提高了工作效率。实现全数焊点100%检查,并建立每台车辆的可追溯焊接质量档案。
结语
通过ai技术对焊接过程中的电阻、电流、热量进行实时监控,提高了焊接质量的判断准确率,达到了83%-85%,大大提高了工作效率。实现全数焊点100%检查,并建立每台车辆的可追溯焊接质量档案。
结语
“焊接”是精密的工艺过程,而“ai”则是智能的科技引擎。结合二者,该企业正利用技术力量挖掘效能潜力,用数据驱动焊接的精准与稳定。ai的助力,帮助优化焊接工艺,大大减轻工作负担,提升工作效率,员工的健康、安全也能得到更有力的保障,开启了汽车智能焊接新篇章!
扫码了解更多树根案例!
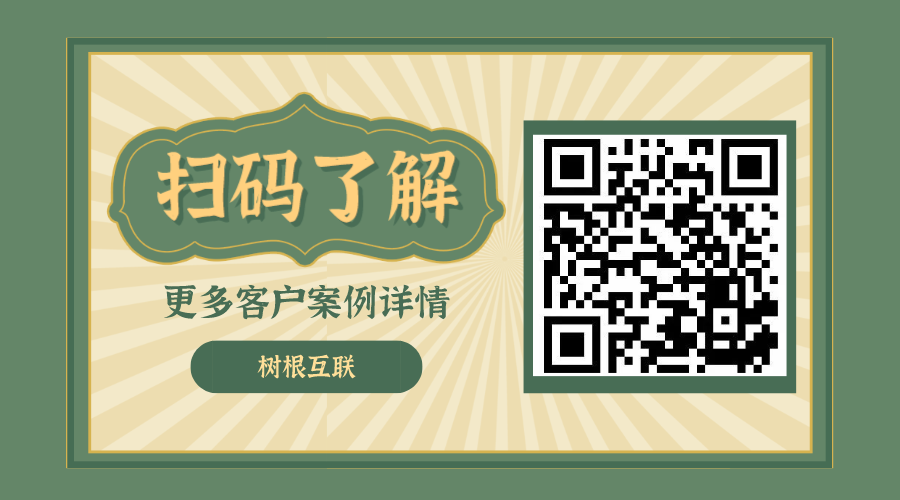