在接受世界经济论坛采访时,三一重工董事长
梁稳根表示:“三一集团要建设好开放的工业互联网平台,为众多的中小企业赋能,也就是为客户赋能,为代理商赋能,为零部件供应商赋能,共同来探索数字化的转型。目前,三一投资的树根互联,就是一个工业互联网平台,旗下平台广泛连接了众多不同类型的工业设备。”
在三一桩机工厂里,由树根互联打造的“根云平台”成为了撬动质量变革、效率变革和动力变革的支点。
经过自动化、数字化、智能化升级后,三一桩机工厂共有8个柔性工作中心,16条智能化产线,375台全联网生产设备。依托由树根互联打造的“根云平台”,实现生产制造要素全连接,整个工厂已成为深度融合互联网、大数据和人工智能的“智慧体”。
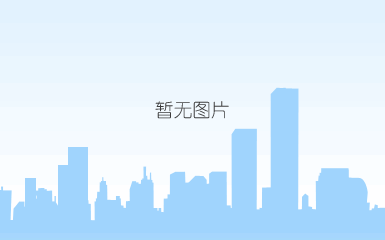
依托树根互联“数字化转型新基座”,三一正在积极地采用包括5g、ar、ai、工业互联网等第四次工业革命带来的前沿的技术,改造和建设一大批聚焦大型装备制造业的灯塔工厂。
此次升级,5大应用场景值得关注:
工匠技术赋能机器人:实现智能化柔性焊接
通过工匠技能和实践经验的参数化及软件化,借助激光传感技术以及自适应算法,实现了机器人在重型装备厚管的柔性焊接,解决了工匠技术传承难、重型装备厚管人工焊接效率低、质量一致性差等管理难题。
机器视觉工业机器人:解决重型装备装配难题
借助2d/3d视觉传感技术、ai算法以及高速的5g网络,通过重载工业机器人、机器视觉及智能纠偏算法的协同,完成二十余种大型、重型动力头的高精度、多定位基准自动化柔性装配,解决了“16吨动力头无人化装配”等难题。
双agv联动重载物流:高效自动化
在精准授时、低时延的5g无线工业专网的保证下,行业首创重载agv双车联动,实现27米超长超重物料的同步搬运和自动上下料。
人机协同:机器人也能成为“老师傅”
人利用手柄操控机器人进行装配,通过力学和视觉反馈,充分融合人的灵活性和机器人的大负荷双重优势。并通过ai技术训练机器人分析最优方式,实现机器人免编程自动柔性装配。
ai iiot:助力设备作业效率提升
桩机工厂里近36000个数据点不断采集数据,结合ai分析与大数据建模,实现了全厂设备互联,设备预测性维护,关键设备动态参数调节和优化。并基于工厂上千台设备及仪表,识别重点耗能设备,实现了能源的精细化管理。
相比于改造前,三一北京桩机工厂在相同厂房面积下产值翻了一番,总体生产设备作业率从66.3%提升到86.7%,平均故障时间下降58.5%。目前,该工厂可生产近30种机型。2020年,三一北京桩机工厂的人均产值已达到1072.8万元。
桩机工厂的蜕变,是三一重工过去3年推进数字化战略转型的一个缩影。“灯塔工厂只是起点,不是终点”, 三一集团董事、高级副总裁代晴华表示,三一重工将继续沿着“ai 工业知识行业”的数字化转型路径大步发展。
未来,三一重工“灯塔工厂”的诸多经验还将对产业链伙伴、行业,乃至整个“中国智造”赋能。而树根互联作为“数字化转型新基座”,也将随之深入制造业的毛细血管之中,加速产业基础高级化、产业链现代化进程。